Good news: American customer purchased 8 units of our waterjet abrasive removal system at one time.
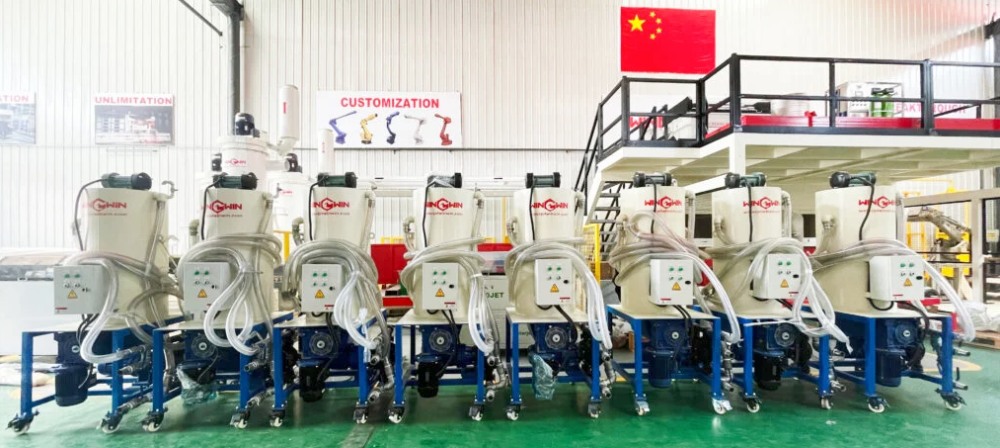
Content:
I. What is the functioning process of the waterjet abrasive removal system?
II. How can one utilize the waterjet abrasive removal system?
III. What are the benefits of the waterjet abrasive removal system?
IV. Is it possible to reuse the abrasives processed by the machine?
Waterjet Abrasive Removal System Garnet Recycling And Removal For Any Brand Water Jet Cutting Machine Waterjet Residual Abrasive Removal System for Waterjet Cutter. Follow our YouTube channel for new waterjet workstation cases.
Struggling to clean up waste abrasive in your waterjet cutting platform's sink?
Unsure of the most efficient cleaning method?
Seeking effective cleaning solutions?
Introducing Win-Win’s automatic waterjet abrasive removal system.
Over time, waste abrasive accumulates in the water sink of a waterjet. When it reaches a certain level, cleaning becomes necessary. In traditional methods, the cutting table work must be halted for manual abrasive removal. This manual process is labor-intensive and demands physical exertion due to the buildup of abrasive and cutting debris resembling thick sediments at the bottom of the water jet tank. This process is time-consuming and strenuous for workers.
Now, with the mobile waterjet abrasive removal system, abrasive can be removed without disrupting regular cutting operations, thanks to its automatic functionality.
Question: How do you operate the auto waterjet abrasive removal system? Is it complex?
Operating the auto waterjet abrasive removal system is straightforward. The machine features four control buttons, with buttons 1 and 2 for starting and pausing. These controls manage the system to suction sewage and impurities from the cutting platform's water tank. Utilizing centrifugal force, the machine separates water from impurities and abrasives, recycling the water back into the tank for continuous use without generating waste. When the impurity level in the system hits a certain point, activating another button initiates the sand discharge mode, expelling dehydrated abrasives and cutting debris.
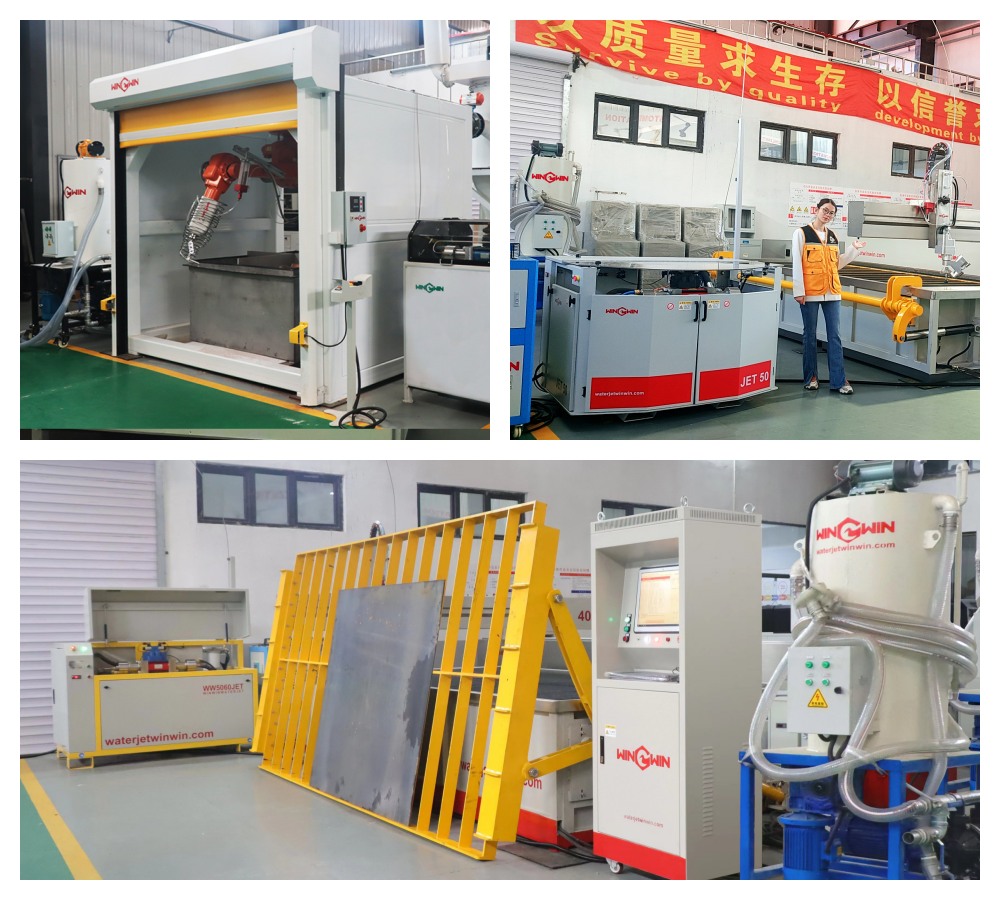
· Efficiently and rapidly eliminate abrasives in oversized sinks
· While the waterjet cutting machine is in operation, the large-scale waterjet abrasive removal system functions automatically without interference.
· Streamlined, cost-effective, and efficient method for abrasive removal, allowing continuous operation of the waterjet cutting machine.
· The unit can be positioned within a 10-meter radius of the waterjet cutting machine.
· A robust suction is generated by the 8 HP diaphragm pump.
· Achieve a flow rate of up to 162 liters per minute.
· Gain the capability to cleanse vast sinks despite limited floor space availability.
· Achieve an abrasive removal rate exceeding 90%.
· Throughout the entire abrasive removal process, the filtered water is continually discharged into the water sink without the need for refilling.
Realize annual cost savings exceeding $8000.00 through comprehensive measures!
FAQ – Can the abrasives processed by the automatic waterjet abrasive removal system be recycled?
In addressing this question, a balanced perspective is essential. While it is technically possible to recycle them, we do not advocate this practice for the following reasons:
Variations in cutting materials necessitate specific abrasive requirements. Some materials demand 60-mesh abrasives, while others may need 80 or 120 mesh. Typically, larger abrasive particles result in faster cutting speeds but may yield a less smooth cutting surface. Conversely, finer abrasives lead to slower cutting speeds but produce exceptionally smooth edges, eliminating the need for additional manual finishing. When abrasives are mixed with high-pressure water and impact the workpiece surface, they break down into finer particles that settle at the tank's bottom, reducing the efficiency of reusing them. While this approach may save on abrasive costs, it hampers cutting efficiency.
The automatic waterjet abrasive removal system not only recycles abrasives but also collects scraps from the cutting process. Separating minute scraps, especially non-metallic ones like glass or plastic, can be cumbersome and time-consuming. While metal scraps such as iron can be separated using magnets, dealing with other materials may not be as cost-effective as purchasing new abrasives.
In summary, while it is theoretically possible to reuse the recovered abrasives from the automatic waterjet abrasive removal system, the operational and time costs make this approach less cost-effective. Therefore, we do not recommend this method.
If you are interested in any waterjet products.