Product Description:
Waterjet On/Off Valve - Seal Buttress Waterjet Replacement :
Item No.: 100062-1
Reference No.: 001337-1|20457978
As part of the on off valve repair kits for high performance waterjet on off valve repair kit
What models of waterjet head parts are this repair kit suitable for?
The on/off valve seal buttress is used on the 302001-1 high performance waterjet repair kit. The whole set repair kit includes:
A. Poppet Landing | 100059-1 |
B. Poppet | 100060-1
|
C. Poppet Seal | 100061-1 |
D. Seal Butress | 100062-1 |
E. Seal Ejection Tool | 100104-1 |
F. Seal O-ring Dark Red | 400042-006 |
G. O-ring | 400043-014 |
Uneven Force Distribution
The unreasonable design of the waterjet replacement can lead to accelerated wear. If there are defects in the replacement design, it will cause unbalanced force distribution. For example, an improper nozzle shape or internal channel design of the replacement can result in uneven impact force of the high-pressure water flow and abrasive when ejected, making some areas of the replacement bear excessive force and thus accelerating the wear rate.
Impact of High Hardness and Toughness Materials
The material of the object to be cut is also a factor contributing to excessive wear of the waterjet replacement. Materials like glass and high-hardness metals have much stronger hardness and toughness compared to others. When the waterjet replacement interacts with these materials, it will increase eddy currents and friction. For instance, when cutting high-hardness metals or glass, the replacement will experience greater resistance and more complex physical interactions, leading to accelerated wear.
Excessive Pump Flow
Using a pump with too large a flow rate can cause excessive water flow, which in turn leads to faster wear of the waterjet replacement. For example, if the water flow is too strong, it will exert greater impact on the replacement, similar to how a powerful current can erode a riverbed more quickly, accelerating the wear of the replacement surface.
Lack of Cleaning and Maintenance
Failing to regularly clean and maintain the waterjet can result in dust and dirt accumulating on the surface of the waterjet replacement. This not only affects the cutting quality but also accelerates the wear rate. Without proper cleaning and maintenance, the replacement may be subject to more friction and potential corrosion due to the presence of contaminants.
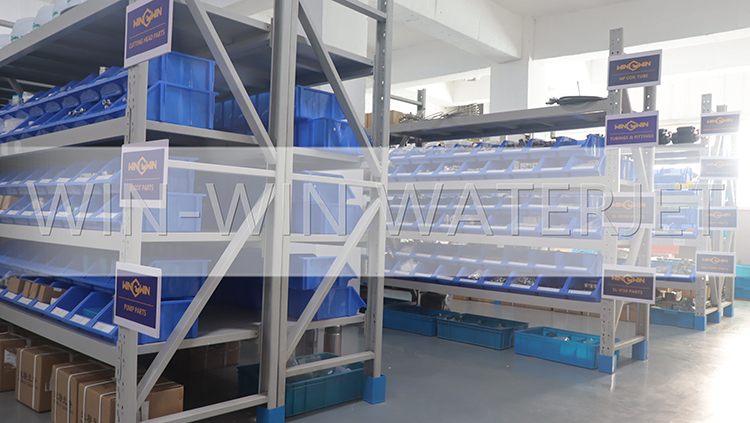
Matching Replacement to Cut Object
Choosing the right waterjet replacement and design according to the material and shape of the object to be cut can effectively reduce the wear rate. For different materials like glass or various metals, specific replacement designs and materials should be selected to ensure better cutting performance and slower wear.
Optimizing Replacement Design
Proper Replacement Selection
In the actual cutting process, selecting the appropriate waterjet replacement type based on the characteristics of the cut object is crucial. Considering factors like material, thickness, and shape can help choose a replacement that is more suitable and reduces unnecessary wear.
Adjusting Cutting Parameters
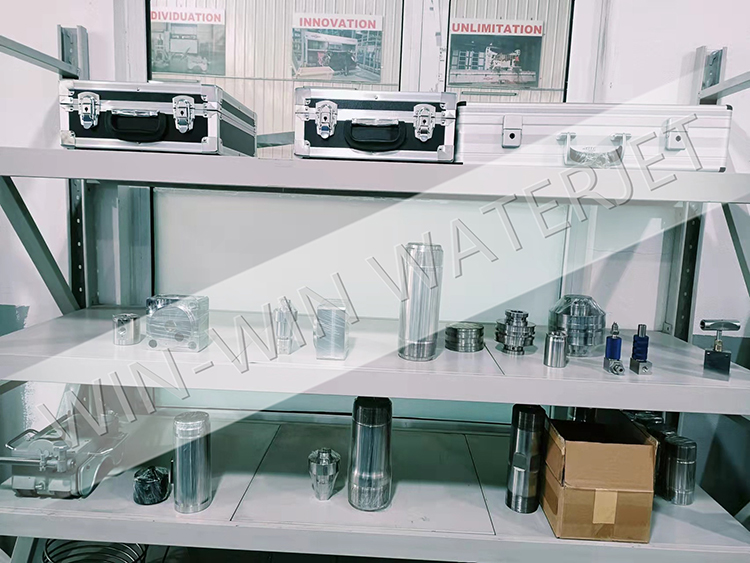
Cleaning the Replacement Surface
Regularly cleaning the surface of the waterjet replacement to remove dust, dirt, and residual abrasive is essential. This can be achieved through appropriate cleaning methods and tools, ensuring the replacement remains in good condition and reducing wear.
Timely Replacement or Repair
In general, the waterjet is a highly efficient and environmentally friendly cutting tool. During use, we must pay attention to the wear condition of the waterjet replacement and adopt corresponding solutions. Only in this way can we ensure the cutting efficiency and accuracy of the waterjet and bring more convenience to our production and life. If the above methods fail to solve the problem of excessive wear of the waterjet replacement, it is necessary to seek professional waterjet maintenance companies. Since the waterjet is a high-precision electromechanical device, it requires experienced technicians for maintenance and should not be disassembled or operated casually.
You can contact us. We will help you solve the problem.